Ilocos, a region in the Philippines, is palpably one of the strongholds of heritage preservation in the country. The numerous traditional arts and crafts of Ilocos Norte and Ilocos Sur have continued to withstand the waves of time for over many hundred years now.
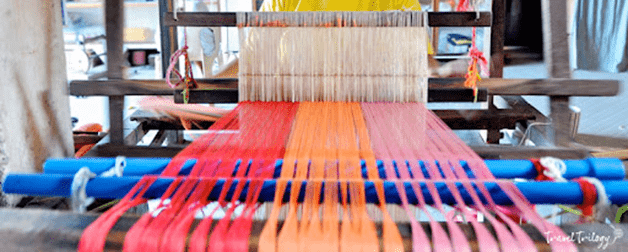
The art of Inabel weaving
Inabel is undoubtedly one of the arts and crafts that the Ilocos region takes pride in. The art of inabel or cotton-loom woven cloth has rooted traditions before the Spanish colonial period. Southeast Asian countries were already trading inabel before the Spaniards acknowledged it for its sturdiness and competed with the Spanish weaving industry.
During the Spanish colonial period, inabel was endorsed as sails for galleons which are large, multi-decked sailing ships. In the same way, it was used locally in boats.
The root word “abel” in the Ilocano dialect means to weave, and inabel translates to ‘woven.’ What sets the abel iloco (or abel iloko) from other woven cloths is its softness, distinct design style, excellent quality, and durability. Inabel or abel iloco is a distinctly Ilocano textile made of cotton that may be plain or patterned.
How is Inabel fabric made?
PREPARING THE YARN
The traditional process of Ilocos weaving begins with picking cotton balls, getting rid of the seeds using a cotton gin, pounding or beating with lagundi sticks, twisting the cotton by a spindle, and winding the cotton yarn into the skeiner. In a skein, the yarn is rolled into a loose, oblong-shaped twist.
The skeined yarn is then brushed with natural dyes from plants and crops like yellow ginger, the indigo plant if you want blue color and the bark of a “sappan” tree for a red color. This combing process will make the skeined yarn durable and glossy. The Ilocano weavers can mix up the primary colors to produce a variety of other colors.
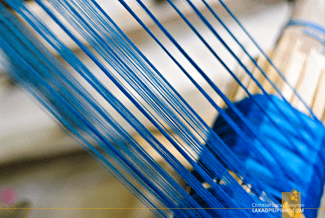
PARTS OF A BASIC LOOM
To grasp the traditional process of Ilocos weaving, we have to be familiar with the loom. A loom is a mechanism or device which is used to produce woven fabric. With this, Ilocano weaver needs to master the intricate and strenuous traditional process of properly synchronizing their hands and feet to use the wooden handloom and hardwood pedal looms. The basic parts of a loom are a warp beam, harness, heddle, shuttle, reed, and cloth roller.
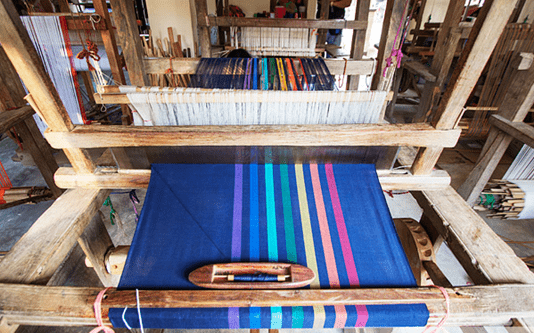
The warp beam holds the warp yarn and is controlled by the local weaver to release warp yarns to the weaving area of the loom. Shaft/harness, a frame that holds the warp threads. More number harness means more patterns can be made.
These shafts can go up or down to allow the weft to cross through and form the desired pattern. Hanging from the shaft of a loom are wires or cords called heddles. A hole within the center of the eye of a heddle each warp yarn goes. Heddles are essential to inabel weaving because they are raised or lowered whenever the shaft is moved.
The device that Ilocos weavers use to carry the weft yarn is called the shuttle. The shuttle releases thread from the bobbin as it passes back and forth through the warp shed and forms the filling cloth.
Reed is a comb-like frame with vertical splits that pushes forward whenever the shuttle passes between the warp yarns and presses back the filling thread in position. Nearest to the local weaver is the cloth roller, where the woven textile is rolled up.
DRESSING UP THE LOOM
The dyed yarns are prepared in a wooden handloom and hardwood pedal looms to produce unique designs and patterns. Local weavers loop the skeined yarn into the bamboo spool then into the warping reel.
Warping is the method of uniting yarns from different cones together to form a sheet. The importance of warping is to preserve the yarn elongation and to maintain it at an even level. With this, better performance during weaving can be accomplished in terms of a low-end breakage rate.
The warp yarn is then wound into the warp beam rod. The local weavers will then insert the warp yarn through the eye of a heddle using a weaving hook. Through the spaces of a reed, Ilocano weavers insert the warp yarn and “dresses” the loom by tying the heddles behind the beater.
THE ART OF ABEL WEAVING
Now that the loom is “dressed,” the Ilocano weaver can start weaving. Plain inabels are the most commonly produced and used. In the Ilocos region, inabels are used for everyday materials such as table runners, hand towels, linens, and more.
Creating inabel truly takes time, but they are worth it all because they have a rewarding beauty. Abel weaving is not just the interlocking of warp or vertical yarns and the horizontal yarns but a coming together of culture, creativity, and skills of Ilocano weavers.
Each cotton thread is carefully counted and intricately arranged according to color before being wrapped into the loom to set up the inabel pattern. Just setting up the pattern takes weeks to execute. There are three popular patterns that you can always see in the Ilocos weaving.
DESIGN TECHNIQUES
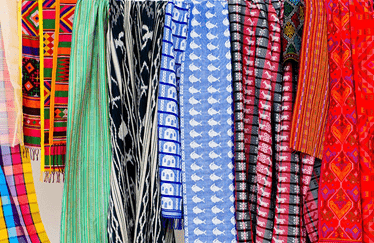
- Binakul Pattern – in Ilocano, binakul or binakol means “twill”. The binakul pattern can be easily recognized by its identical, intertwined geometric that can also be described as a dizzying pattern. It is meant to protect the wearer, fend off and distract evil spirits, thus, its dizzying pattern. That dizzying pattern is said to protect the wearer, fend off and distract evil spirits.
- Pinilian or Brocade Weave – the word pinilian means “chosen,” This type of abel weaving is characterized by refined brocade weave. This Ilocos weaving technique creates designs that “floats” on the threads by inserting sticks on chosen wrap threads.
- Ikat Tye Dye Technique – before weaving the fabric, the yarn is wrapped in bundles and dyed. The areas that are tied together leave colorless patches. A mix of indigenous plants is used as natural dyes and boiled until the color that the weaver needs is attained.
One of the oldest loom weaving centers in the Ilocos region is Cristy’s Loom Weaving in Barangay Camangaan, Vigan City. It was founded by Cristy Antinaja and is now passed down to her granddaughter. To many Ilocanos, weaving is not just an expression of art but also a source of livelihood.
In the present time, most fabrics are being mass-produced, and the traditional process of abel weaving is slowly deteriorating since the number of Ilocos weavers is declining. The younger generation is encouraged to keep the art of inabel alive.
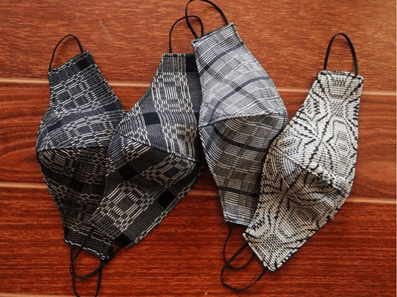
Though challenged by the threads of time, abel Iloco strives to adapt and continue to be part of the current Ilocano culture. Today’s abel products are not limited to being home linens. Still, they are also made into trendy bags, designer clothes, beautiful jewelry, protective masks, and the like.
Abel Iloco is truly an embodiment of Ilocanos’ rich culture. If you want to visit the north and know more about its culture, you might want to check the best destinations in Ilocos Norte. For your home options up north, you may check out Camella’s house and lot for sale in Ilocos Norte. You may also visit our house catalog or our selections of property for sale nationwide.
By: Sharmaine Aguinaldo